FAQ
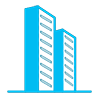
What about samples?
We offer free samples. However, the shipping fees will need to be covered by you. The cost of shipping the sample depends on its weight, packaging size and your location.
What about customization?
We do provide product customization services, however, there are certain requirements that need to be met. This includes meeting the minimum order quantity and covering the costs of sample proofing and shipping. If you meet the minimum order quantity with your first order, then the proofing fee can be applied towards your order payment. However, if the minimum order quantity is not met or no order is placed, you will be responsible for the proofing fee. For more information, please feel free to contact our customer service team.
What about shipping?
We typically ship regular products within 7 days of your order being placed. However, the shipping time for customized or non-standard products may vary depending on the specific situation.
What about logistics?
We have established a long-term partnership with freight forwarders, which enables us to provide discounted transportation plans tailored to the characteristics of your products. However, if you already have a preferred freight forwarder, we are more than happy to use their services for transportation.
What about after-sales service?
Should you encounter any issues with the product quality, please reach out to our customer service team promptly and include pictures or videos of the product that requires after-sales service. Once we have confirmed the issue, we will strive to provide you with a satisfactory solution tailored to your specific situation.
What about customer service?
Our customer service team is comprised of highly skilled and efficient professionals who are readily available to assist you with any inquiries, both prior to and following your purchase. It is our pleasure to be of service to you!
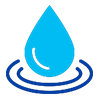
What is UV curable ink?
UV curable ink is a special type of ink that can be quickly dried and cured using ultraviolet (UV) light. It offers advantages such as fast curing, no solvent volatilization, and environmental friendliness.
What are the application areas for UV curable ink?
UV curable ink is widely used in printing and coating applications, and is suitable for use on a range of materials, including paper, plastic, metal, glass, ceramics, and more. Common uses include labels, packaging, promotional items, electronic products, etc.
What are the advantages of UV curable ink compared to traditional ink?
UV curable ink cures rapidly without long drying time, enabling efficient high-speed production and quick delivery. Additionally, UV curable ink does not produce harmful solvent emissions, making it an environmentally-friendly option. It also has good wear and light resistance.
How is the curing process of UV curable ink controlled?
The curing process of UV curable ink is controlled by adjusting the irradiation time and intensity of the ultraviolet light. This needs to be tailored based on factors such as the ink type, material being printed/coated, and the desired effect. Typically, a control system on the light-curing equipment is employed to set and monitor the curing conditions, ensuring optimal curing results.
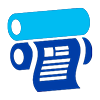
How do I choose the right flexographic plates for printing?
Firstly, we need to take into account your specific needs and printing requirements. Different flexographic printing plate materials are suitable for different types of printing jobs. For instance, if you need to print images with high resolution and detail, you may need to select a flexographic material that offers higher resolution.
Secondly, we can consider your printing equipment and plate-making process. Different plate-making systems and equipment may have specific requirements for flexographic materials. You should ensure that the selected flexographic material is compatible with your equipment and can deliver good performance and results in your plate-making process.
Additionally, you could also take into consideration the durability and service life of flexographic materials. Some flexographic materials have a longer lifespan and can be reused multiple times without compromising print quality. This could be particularly important for high-volume printing and frequent use cases.
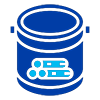
What is the purpose of using varnishes?
Varnishes are used to improve the texture and appearance of printed materials, accentuate their glossiness, and make colors more vivid. They also enhance the durability and water-resistance of paper, thereby increasing the service life of printed materials.
How do you select the appropriate varnishes?
To choose the right varnish, you must consider the unique requirements of the printed materials and the conditions they will be subjected to. Different types of varnishes have varying attributes such as glossiness, wear resistance, and drying time. Therefore, it is essential to select the appropriate type and formula of varnish relevant to the properties of the specific paper product.
What are the application methods of varnishes?
Coating or spraying are typical ways of applying varnish onto paper surfaces. Coating can be done by using a roller or blade coating machine, while spraying involves evenly applying the varnish onto the paper using a spray device.
How long does it take for varnishes to dry on paper?
The drying time of varnish varies depending on several factors, including the formula of the varnish, the thickness of the coating, and the ambient conditions. Generally, the drying time ranges from a few minutes to several hours, but full curing may require an extended duration.
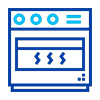
What are the different areas where plate making equipment is used?
Plate making equipment is widely used in the printing industry for various applications like packaging printing, label printing, commercial printing, and others. This equipment can produce different types of printing plates such as flexographic plates, photopolymer plates, CTP plates, etc.
How does plate making equipment work?
The working principle of plate making equipment involves three main steps: light exposing, developing, and curing. Firstly, the design pattern is transferred onto the photosensitive material in the photosensitive device. Then, the photosensitive material is processed using the development device to reveal the pattern. Finally, the printing plate is cured using appropriate techniques in the curing device to ensure its durability and print quality.
What skills are required to operate plate making equipment?
To operate plate making equipment, you need to have certain technical and operational knowledge. Operators must understand the working principle, operating procedures, safety regulations, and be able to debug and troubleshoot issues. Additionally, having some graphic design skills can help in creating high-quality printing plates.
How do you maintain and upkeep plate making equipment?
Maintaining and taking care of plate making equipment is essential to keep it running smoothly and prolong its lifespan. Common maintenance tasks include cleaning the equipment, replacing consumables and parts, performing regular inspections, calibrating the equipment, etc. Operators should follow the guidelines provided by the equipment manufacturer and perform periodic maintenance and upkeep work.